提高五金冲压件的使用寿命是一个系统工程,涉及材料、设计、工艺、模具、润滑等多个环节的优化。以下是一些关键策略:
1.优化材料选择与预处理:
选材:根据零件的服役条件(如受力状态、环境、耐磨性、耐腐蚀性要求)选择合适的材料牌号(如不同强度等级的不锈钢、碳钢、铝合金、铜合金等)。考虑材料的成形性能、强度、韧性、疲劳ji限和耐腐蚀性。
材料质量控制:确保原材料厚度均匀、表面质量良好(无严重划痕、氧化皮、锈蚀)、力学性能稳定。使用前进行必要的检验。
材料预处理:进行适当的预处理,如清洗去除油污、磷化或钝化处理以提高润滑性和耐蚀性,或进行退火处理(尤其对硬化材料)以改善成形性并减少残余应力。
2.科学合理的结构设计:
避免应力集中:设计圆角过渡,避免尖锐的棱角和急转弯。圆角半径应足够大,以分散应力,防止疲劳裂纹萌生。
优化几何形状:合理设计加强筋、凸台、翻边的位置和形状,使其既能满足功能要求,又能提高结构刚度和强度,减少变形和振动。
布局优化:优化排样设计,尽量减少废料,同时确保材料纤维方向有利于关键部位的受力,避免在关键区域出现冲裁毛刺面。
3.精密冲压工艺控制:
的冲裁间隙:根据材料类型和厚度,设定并保持凸模与凹模之间的间隙。间隙过大导致毛刺大、断面质量差;间隙过小则加速模具磨损,增加冲裁力,易产生二次剪切和毛刺。
优化工艺参数:控制冲压速度、压边力(在拉深、胀形等工序中)、顶出力等。合适的压边力能有效防止起皱又不至于导致材料过度减薄或拉裂。
多工序合理规划:对于复杂零件,合理规划冲裁、弯曲、拉深、翻边、等工序的顺序和组合方式(如使用级进模、传递模),避免因工序安排不当导致材料硬化过度或产生内部损伤。
4.高质量模具与维护:
模具材料与热处理:选用高耐磨性、高韧性、热稳定性好的模具钢(如硬质合金、高速钢、粉末冶金钢等),并进行恰当的热处理(如淬火、回火)和表面强化处理(如TD处理、PVD/CVD涂层、渗氮等),大幅提高模具的耐磨性、抗咬合性和疲劳寿命。
模具精密制造:确保模具加工精度高,型面光洁度好,配合间隙均匀。
模具维护保养:建立严格的模具维护保养制度,包括定期清洁、检查、润滑、修复磨损部位(如刃磨、更换易损件)。防止模具带伤运行。
5.有效的润滑与冷却:
选用合适润滑剂:根据工序(冲裁、弯曲、拉深)、材料、变形程度选择合适的润滑剂类型(油基、水基、固体润滑剂等)。润滑剂需具备良好的减摩、抗磨、散热、防锈性能,并易于清洗(如后续需电镀或喷涂)。
正确涂布润滑剂:确保润滑剂均匀、适量地涂布在材料表面或模具工作区域,避免局部润滑不足导致划伤或咬合。
冷却措施:在高速冲压或难成形材料加工中,采用有效的冷却系统(如模具内冷却水道)控制模具温度,防止热变形和热疲劳。
6.严格的质量控制与检测:
首件检验与过程抽检:严格执行首件检验制度,并在生产过程中定期抽检关键尺寸、外观(毛刺、划痕、变形)、功能性(如装配性)。
过程监控:利用SPC等统计过程控制方法监控关键工艺参数的稳定性。
成品检验与测试:对成品进行必要的性能测试(如盐雾试验、硬度测试、疲劳测试)以确保符合使用寿命要求。
总结:提高冲压件寿命的关键在于控制(材料、设计)、过程优化(工艺、模具、润滑)和质量保障(检测、维护)的紧密结合。每个环节的精益求精都能显著减少应力集中、磨损、疲劳和腐蚀失效的风险,从而终实现产品使用寿命的有效提升。
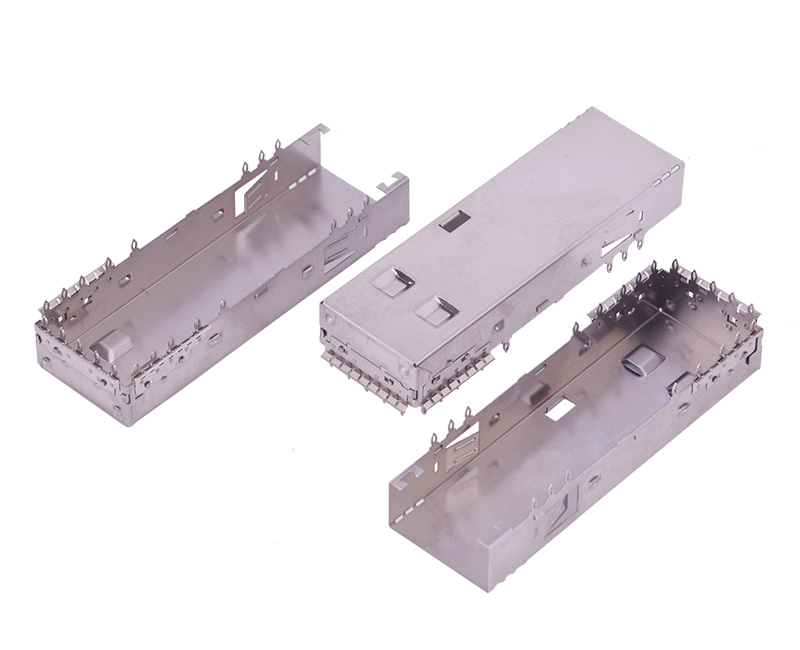
上一条:五金冲压件加工中的成本控制:材料损耗率与工时优化实战
下一条:没有了